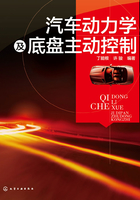
2.3 汽车制动性能
汽车行驶时能在短距离内停车且维持行驶方向稳定性和在下长坡时能维持一定车速的能力,称为汽车的制动性。
汽车的制动性是汽车的主要性能之一。制动性直接关系到行车安全,重大交通事故往往与制动距离太长、紧急制动时发生侧滑等情况有关,故良好的汽车制动性是汽车安全行驶的重要保证。
2.3.1 基本方程
制动性能分析的基本方程可根据牛顿第二定律直接写出。参照图1-3,制动时x方向的运动方程为
(2-31)
式中 Dx——制动减速度;
Fbf——前轴制动力;
Fbr——后轴制动力。
前、后轴的制动力主要由制动器转矩引起,并综合了滚动阻力、轴承摩擦和传动系内摩擦阻力等的影响。若要全面分析制动减速度,首先须详细分析作用在车辆上的各个力。以下就减速度为常数的特殊情况加以分析。
制动减速度为常数时,有
(2-32)
式中 Fxt——作用在车辆上的所有纵向力之和;
u——向前的速度。
若ts时间内车辆速度由u0降为uf,考虑到Fxt为常数,对上式积分则有
(2-33)
(2-34)
由于速度和距离之间存在u=dx/dt的关系,用dx/u替代式(2-33)中的dt并积分,得到速度与距离之间的关系为
(2-35)
式中 s——减速过程的行驶距离。
当制动初始速度为u0、终了速度uf为零时,定义SD为制动距离,则
(2-36)
而制动时间为
(2-37)
因此,其他条件相同时,制动时间与制动初速成正比,而制动距离与制动初速度的平方成正比。
制动过程中车辆动能被制动系吸收。当高速行驶的汽车紧急制动时,被吸收的动能E相当多。E与汽车质量成正比。
(2-38)
在制动的不同阶段,被制动系吸收的能量多少是不同的,每一瞬时都取决于制动力与车速的乘积。制动开始时吸收的能量最多,随后逐渐减少。制动时间内平均吸收的能量称为制动功率,它等于制动能量E除以制动时间,即
(2-39)
制动功率的计算对制动系设计是很有用的。举个例子来说,一个质量为1350kg的轿车从130km/h制动至停车需要吸收约880kN·m的能量。假如制动时间为10s(制动减速度为3.61m/s2),这一时间内制动器平均吸收功率约为88kW。一辆满载质量为32t的货车在100km/h的初速下紧急制动时,需要将数以千计甚至上万千瓦的能量耗散掉。
2.3.2 制动力
如无特殊声明,制动力一般指制动减速过程中地面作用于轮胎、与汽车速度方向相反的力。使汽车产生制动减速的力有多个根源,虽然制动器是产生制动力的主要根源,但下面将首先讨论其他原因。
(1)滚动阻力
滚动阻力的方向总与汽车运动方向相反,因此它产生一部分制动力。滚动阻力的大小为
(2-40)
总的滚动阻力与轴荷分布(静载或动载)没有关系。滚动阻力通常可提供大约0.01g的减速度。
(2)空气阻力
空气阻力取决于空气动压力,因此与速度的平方成正比。低速时空气阻力可忽略。在通常的公路行驶速度下,空气阻力可提供大约0.03g的减速度。
(3)动力传动装置阻力
发动机、变速箱和主减速器的内摩擦及惯性作用都会对制动产生影响。在讨论加速性能的时候知道,这些零件使车辆的有效质量增加。制动时,动力装置的惯量相当于增加了驱动轮的转动惯量。动力传动装置的阻力是由变速箱和主传动中的轴承摩擦、齿轮摩擦和齿轮的搅油损失以及发动机制动等引起。发动机制动是由其内摩擦和泵气损失引起(当发动机转速超过某一高速时,会引起飞车从而导致发动机的制动作用消失)。对于装有手动变速器的汽车,如果制动过程中离合器处于接合状态,发动机制动将被放大,放大的倍数等于当前工作挡位的传动比。对于带液力变矩器的自动变速箱,动力流反方向传递时,经变速箱传到发动机的转矩是很小的,因此对此类汽车来说发动机制动力对整车制动的影响并不大。
动力传动装置的阻力能否帮助制动取决于减速度的大小。动力传动装置的旋转零件在其内部阻力作用下会越转越慢,如果车辆速度下降得更快,那么驱动轮上制动器产生的制动力矩就有一部分要消耗在动力系统旋转零件的减速上。反过来,如果车辆速度下降得不快,动力传动装置的阻力可能足以在驱动轮上产生所需要的制动力矩。
(4)坡度
道路坡度对制动力有直接影响——下坡时减小制动力、上坡时增加制动力。坡度产生的制动力为
(2-41)
当坡度角较小时,坡度角与坡度近似相等。因此,一个4%(0.04)的坡将产生大约±0.04g的减速度。
2.3.3 制动器及其制动力矩
汽车常用的制动器有两种型式——鼓式和盘式,如图2-13所示。

图2-13 鼓式和盘式制动器
由于鼓式制动器的制动效能较高且易于兼用作驻车制动器,以前汽车上更多地采用这种制动器。鼓式制动器的缺点是其制动力矩的恒定性没有盘式制动器好。盘式制动器的制动效能低,要求施加更大的促动力,通常采用这种结构的汽车需添加制动助力装置,如真空助力器。如果所有制动器皆为盘式,就需要单独设置驻车制动器。
鼓式制动器的领蹄具有增势作用,它使得用较小的促动力获得较大的制动力矩。制动效能定义为制动器制动力矩与制动轮缸压力之比。图2-14所示为领从蹄鼓式制动器的结构简图和工作原理。制动器由两个蹄片组成,它们通过转动销支撑在制动底板的底部。施加促动力Pa使摩擦片靠紧在制动鼓上从而产生摩擦力,其大小为正压力乘以摩擦片材料与鼓的摩擦系数(μ)。对领蹄A的铰支点求力矩平衡得
(2-42)

图2-14 领从蹄式鼓式制动器蹄上的作用力
领蹄上产生的摩擦力大小为
(2-43)
联立式(2-42)和(2-43),得
(2-44)
同样地,对于从蹄有
(2-45)
在双领蹄、双从蹄和领从蹄三种制动器中,双领蹄式制动器的制动效能最高。制动效能越高,则摩擦片摩擦系数越敏感,产生噪声和啸叫的可能也越大。由温度变化、磨损或其他因素引起μ的较小变化会导致制动器表现得飘忽不定。因为盘式制动器没有这种自增势效应,它们通常有更好的力矩恒定性,虽然要以更大的促动力为代价。
制动器产生的制动力矩一方面产生地面制动力,另一方面使车轮和传动系减速。它们之间有如下关系。
(2-46)
式中 Fxb——地面制动力;
Tμ——制动器制动力矩;
Iw——车轮(及传动系旋转零件)的转动惯量;
w——车轮角减速度。
当轮胎近似于纯滚动时,车轮角减速度与车辆减速度之间的关系为w=ax/r,且为了计算方便将转动惯量Iw并入整车质量考虑。这种情况下,制动器制动力矩与地面制动力的关系为
(2-47)
2.3.4 轮胎与路面之间的摩擦
只要轮胎作滚动,地面制动力就应按式(2-47)的关系变化。然而制动力的增加是要受到轮胎与地面摩擦极限限制的。
如图2-15所示,有两种主要的机理可以解释上述摩擦作用的产生。表面黏着力由橡胶与路表混凝土分子间的束缚力引起。在干燥路面,黏着力构成了摩擦力的主要成分;当路面有积水时,黏着力下降较多,因此在湿路面上会失去一部分摩擦力。

图2-15 轮胎与路面摩擦的机理
当轮胎在路表混凝土上滑动时,轮胎变形使得其橡胶中产生能量损失,这可以解释为迟滞作用。迟滞摩擦受路面积水的影响不大,因此若胎面含有高迟滞特性的橡胶,则这种轮胎在湿路面上有更好的附着性能。
黏着和迟滞摩擦都与轮胎—路面接触印迹内的一些轻微滑移有关。当胎面发生变形并产生持续的制动力时,部分(或全部)橡胶单元发生滑移,如图2-16所示。橡胶单元进入接触区之前未发生变形。每一个橡胶单元在移至轮胎接地中心的过程中,径向变形逐渐增加,所受到的地面切向力也增加。向后的切向力使得橡胶单元产生切向变形。当制动强度增加到某一极限时,胎面接触区后部的橡胶单元将首先相对于地面产生滑动。橡胶单元产生滑动后,它产生的制动力会下降。当制动强度进一步增加达到另一极限时,胎面接触区的所有橡胶单元都将相对于地面产生滑动。

图2-16 接触印迹内的制动变形
以上分析说明了制动力与轮胎的滑移是密不可分的。制动力(用制动力系数表示,定义为纵向力与法向力之比Fx/Fz)与滑移率的函数关系如图2-17所示。轮胎滑移率s定义为接触区滑移速度与轮胎向前速度之比。
(2-48)

图2-17 制动力与滑移率的关系
滑移率低于10%~20%时,由黏着和迟滞摩擦引起的制动力系数随之增加。湿路面条件下,黏着摩擦力的减少使得总制动力系数较低。峰值系数φp是一个重要参数,它反映了特定轮胎—路面条件下能够获得的最大制动力。滑移率更大时,制动力系数减小,并在滑移率为100%时达到最小值。滑移率100%意味着车轮抱死,此时的制动力系数用φs表示。φp对应于制动过程能够获得的最大制动力,但这只具有理论上的可行性,因为在峰值附着系数这一点系统是不稳定的。假如制动力矩输出增加到某个值时,它使车轮滑移率达到φp。此时,任何使制动力矩稍有增加的扰动都会使车轮的减速加剧。滑移率增加后制动力降低,反过来使车轮减速得更快并迅速抱死。滑移率增加越过φp后,只有减小制动压力(比如ABS控制时)才能使车轮回到φp工作点。
(1)速度的影响
在干路面上,峰值附着系数和滑动附着系数都随速度增加而降低。因为高速时难以将轮胎印迹内的水排走,湿路面条件下对速度更加敏感。当速度足够高、积水层足够厚时,轮胎将完全漂浮在水膜上面而与路面毫不接触。这就是滑水现象。
(2)充气压力的影响
在干路面,充气压力对峰值附着系数和滑动附着系数只是略有影响。然而在湿路面,充气压力增加时可以使这两个系数提高很多。
(3)垂直载荷的影响
无论在干路面还是湿路面,增加垂直载荷都将肯定使附着系数减少。这是因为载荷增加时,峰值摩擦力和滑动摩擦力并不成比例地增加。一般来说,在轮胎标定载荷附近,载荷每增加10%,这两个附着系数将按1%的量级减少。
2.3.5 制动力比例分配
简单地说,车辆能够获得的制动减速度就是在某一车轴即将达到抱死之点的制动踏板力与制动器增益(制动力矩/制动压力)的乘积。抱死将减少该车轴的制动力,并导致部分丧失对车辆的控制能力。众所周知,最好将制动系设计成前、后轮同时达到抱死点。但要使车辆在所有使用工况下都做到这一点又是不可能的。对于车辆基础制动而言,前、后轴制动力输出的平衡是通过使前、后制动压力符合比例关系获得的。按比例关系调整前、后轴制动力矩的输出就将获得可能的峰值附着力。
车轴峰值附着力的大小主要取决于其瞬时载荷和峰值附着系数。当制动减速度为Dx时,前、后轴荷分别为
(2-49)
(2-50)
式中,为制动过程中的动态载荷转移。
因此,前、后轴的最大制动力分别为
(2-51)
(2-52)
式中 μp——峰值摩擦系数。
以上两式说明前、后轴的最大制动力与减速度有关。图2-18就是根据这两个式子得到的典型轿车在高附着路面和低附着路面的最大制动力变化图。如果施加在某个车轴上的制动力(制动器制动力矩除以车轮半径)超出图中的界限值,将导致该轴抱死。

图2-18 最大制动力随减速度的变化
为求出制动减速度,分别将以下两式
(2-53)
(2-54)
代入式(2-51)和式(2-52)得到前、后轴的最大制动力为
(2-55)
(2-56)
可见,前轴的最大制动力与后轴的制动力有关。这是因为当其他条件相同时,前轴最大制动力取决于载荷前移量,而载荷前移量取决于后轴的制动力。同样地,后轴的最大制动力与前轴的制动力有关。前、后制动力的关系如图2-19所示。

图2-19 前、后轴的最大制动力
图中横坐标代表后轴制动力,它通常与后轮制动压力(与基础制动系的力矩—压力关系对应)成正比。纵坐标为前轴制动力,也与制动压力成正比。令式(2-55)和式(2-56)中另一轴的制动力为零,就得到各直线的起点。
前轴最大制动力随后轴制动力增加而增加,变化率为。后轴最大制动力随前轴制动力增加而减少,变化率为-
。图中的最大制动力线的变化率(绝对值)随路面附着系数或重心高度的增加而增加。车辆载荷条件发生变化时,图中各线的起点平移一个位置。两条最大制动力线的交点可由式(2-55)和式(2-56)联立求解得到。将该点的坐标设为Fxfi和Fxri,可看出它们为
(2-57)
(2-58)
如果制动时企图使制动力位于前轮制动力界线的上方,前轮就会抱死,从而失去转向能力。同样地,如果制动力落在后轮制动力界线的右边,后轮就会抱死,这会使车辆处于不稳定状态。不稳定可能带来不安全,设计制动系时必须加以仔细考虑。
图2-19中,减速度与前、后制动力之和成正比。因而,只要前、后制动力之和相等,不管前、后制动力各自的大小怎样,都产生相同的减速度。如果前、后制动力采用同样的尺度,把产生相同减速度的点连接起来就得到一条45°斜线。
如果要求在附着系数为0.81的路面上获得6.1m/s2的减速度,只要前、后制动力之和落在图2-19示由μ=0.81的最大制动力线和6.1m/s2的减速度线围成的三角形区域内就可以了。
制动力比例分配反映了前、后制动力之间的关系,而制动力由制动器的轮缸压力及其增益决定。可以用一条过原点的曲线反映前、后制动力的分配,这条指向右上方的线称为比例线。如果制动力的比值保持不变或为定值或常数,比例线为一条直线。
制动系设计要解决的主要问题是如何选择制动力比例系数(图中比例线的斜率)以满足各项设计目标,尽管路面附着、前/后轴荷分配、重心高度和制动工况会发生变化。如要满足有关制动法规的要求,必须合理地分配前、后轮制动力。
影响制动力分配的主要因素是前、后轮制动器的增益。单个车轮的制动力可用下式表示。
(2-59)
式中 Gb——制动器增益,它定义为Tμ与Pwc的比值。
实际很难在车辆所有工况下都获得良好的制动性能。下面以图2-20为例来说明制动力分配的复杂性。从该图可看出装载条件(轻载和满载)和路面附着条件的变化。图中画出了美国FMVSS 105干路面制动试验所要求的制动力界线和制动减速度。此外,还画出了湿路面的类似界线。湿路面条件下,假设减速度性能目标为0.25g。

图2-20 多种制动工况下的前、后制动力图
为了实现所有的设计目标,制动力分配线必须通过图中所示的所有三角形区域。这对于前、后制动力为固定比值的汽车来说无法实现,因为这种汽车的制动力比例线是一条直线,而没有一条直线能经过上述所有三角形区域。解决的办法是在制动系中安装一个阀,它使后轮轮缸压力在一定工作压力范围内发生变化。这样的阀就是比例阀。通常使用的比例阀在达到一定压力之前,提供给前、后轮轮缸的压力是相等的。达到该压力之后,比例阀减小对应制动器轮缸压力的增长速率。标记为“500/0.3”的比例阀意思是在压力增加到500psi(1psi=6894.76Pa)之前,前、后制动器的压力是相等的。超过该压力之后,后轮压力增长速率仅为前轮的30%。
比例阀使前、后制动力的分配满足干路面所有制动工况的性能要求,因为比例线通过了所有代表制动性能的三角形区域。唯一的例外是满载时在低附着系数路面的制动,此时减速度达不到0.25g。各种情况下,该图表明前轮首先抱死。
对于货车来说要获得合理的制动力调节更困难,这是因为它的满载和空载工况差别很大。一般来说,反映性能的三角形在这些工况下并不重合,比例调节无法满足所有要求。当然也会有一些解决办法。使用较多的是感载比例阀,惯性比例阀有少量采用。最后,ABS(防抱制动系统)为制动力的自动调节提供了根本的解决方法,目前已被广泛采用。