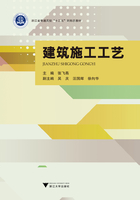
2.1 地基处理工程施工
地基是指建筑物下面支承基础的土体或岩体。地基的主要作用是承托建筑物的上部荷载。地基不是建筑物本身的一部分,但与建筑物的关系非常密切。它对保证建筑物的坚固耐久具有非常重要的作用。
地基有天然地基和人工地基两类。其中,天然地基是指不需要对地基进行处理就可以直接放置基础的天然土层;人工地基是指天然土层的土质过于软弱或不良的地质条件,需要人工加固处理后才能修建的地基。地基处理即为提高地基承载力,改善其变形性质或渗透性质而采取的人工处理地基的方法。
在建筑工程中遇到工程结构的荷载较大,地基土质又较软弱(强度不足或压缩性大),不能作为天然地基时,可针对不同情况,采取各种人工加固处理的方法,以改善地基性质,提高承载力,增加稳定性,减少地基变形和基础埋置深度。
2.1.1 地基处理方案
在建筑学中,地基的处理是十分重要的,地基对上层建筑是否牢固具有无可替代的作用。建筑物的地基不够好,上层建筑很可能倒塌,而地基处理的主要目的是采用各种地基处理方法以改善地基条件。
在选择地基处理方案前,应完成下列工作:
(1)搜集详细的岩土工程勘察资料、上部结构及基础设计资料等。
(2)结合工程情况,了解当地地基处理经验和施工条件,对于有特殊要求的工程,尚应了解其他地区相似场地上同类工程的地基处理经验和使用情况等。
(3)根据工程的要求和采用天然地基存在的主要问题,确定地基处理的目的、处理范围和处理后要求达到的各项技术经济指标等。
(4)调查邻近建筑、地下工程和有关管线等情况。
(5)了解建筑场地的环境情况。
在选择地基处理方案时,应考虑上部结构、基础和地基的共同作用,并经过技术经济比较,选用处理地基或加强上部结构和处理地基相结合的方案。
地基处理方法的确定宜按下列步骤进行:
(1)根据结构类型、荷载大小及使用要求,结合地形地貌、地层结构、土质条件、地下水特征、环境情况和对邻近建筑的影响等因素进行综合分析,初步选出几种可供考虑的地基处理方案,包括选择两种或多种地基处理措施组成的综合处理方案。
(2)对初步选出的各种地基处理方案,分别从加固原理、适用范围、预期处理效果、耗用材料、施工机械、工期要求和对环境的影响等方面进行技术经济分析和对比,选择最佳的地基处理方法。
(3)对已选定的地基处理方法,宜按建筑物地基基础设计等级和场地复杂程度,在有代表性的场地上进行相应的现场试验或试验性施工,并进行必要的测试,以检验设计参数和处理效果。如达不到设计要求,应查明原因,修改设计参数或调整地基处理方法。
常用的地基处理方法有换填法、强夯法、排水固结法、砂石桩法、水泥土搅拌法、高压喷射注浆法、预压法、夯实水泥土桩法、水泥粉煤灰碎石桩法、石灰桩法、灰土挤密桩法和土挤密桩法、柱锤冲扩桩法、单液硅化法和减液法等。
常用地基处理方法分类、作用、原理及适用范围如表2-1所示。
表2-1 地基处理方法分类

2.1.2 换填法
换填法也称换土垫层法,是将在基础底面以下处理范围内的软弱土层部分或全部挖去,然后分层换填密度大、强度高、水稳定性好的砂、碎石或灰土等材料及其他性能稳定和无侵蚀性的材料,并碾压、夯实或振实至要求的密实度。如图2-1所示。换填垫层按回填的材料可分为砂(或砂石)垫层、碎石垫层、粉煤灰垫层、干渣垫层、土(灰土、二灰)垫层等。换填法可提高持力层的承载力,减少沉降量。其常用机械碾压、平板振动和重锤夯实进行施工。

图2-1 换填法
换填垫层适用于浅层软弱土层(淤泥质土、松散素填土、杂填土、浜填土以及已完成自重固结的冲填土)或不均匀土层的地基处理。
换填垫层的厚度应根据置换软弱土的深度以及下卧土层的承载力确定,厚度宜为0.5~3m。(详见《建筑地基处理技术规范》(JGJ79—2012))
1.垫层材料
垫层材料的选用应符合下列要求:

2-1 JGJ792012建筑地基处理技术规范
(1)砂石。宜选用碎石、卵石、角砾、圆砾、砾砂、粗砂、中砂或石屑,应级配良好,不含植物残体、垃圾等杂质。当使用粉细砂或石粉时,应掺入不少于总重30%的碎石或卵石。砂石的最大粒径不宜大于50mm。对湿陷性黄土地基,不得选用砂石等透水材料。
(2)粉质黏土。土料中有机质含量不得超过5%,且不得含有冻土或膨胀土。当含有碎石时,其粒径不宜大于50mm。用于湿陷性黄土或膨胀土地基的粉质黏土垫层,土料中不得夹有砖、瓦和石块等。
(3)灰土。体积配合比宜为2︰8或3︰7。石灰宜选用新鲜的消石灰,其最大粒径不得大于5mm。土料宜选用粉质黏土,不宜使用块状黏土,且不得含有松软杂质,土料应过筛且最大粒径不得大于15mm。
(4)粉煤灰。选用的粉煤灰应满足相关标准对腐蚀性和放射性的安全要求。粉煤灰垫层上宜覆土0.3~0.5m。粉煤灰垫层中采用掺加剂时,应通过试验确定其性能及适用条件。粉煤灰垫层中的金属构件、管网应采取防腐措施。大量填筑粉煤灰时,应经场地地下水和土壤环境的不良影响评价合格后,方可使用。
(5)矿渣。宜选用分级矿渣、混合矿渣及原状矿渣等高炉重矿渣。高炉的松散重度不应小于11kN/m3,有机质及含泥总量不得超过5%。垫层设计,施工前应对所选用的矿渣进行试验,确认性能稳定并满足腐蚀性和放射性安全的要求。对易受酸、碱影响的基础或地下管网不得采用矿渣垫层。大量填筑矿渣时,应经场地地下水和土壤环境的不良影响评价合格后,方可使用。
(6)其他工业废渣。在有充分依据或成功经验时,也可采用质地坚硬、性能稳定、透水性强、无腐蚀性和无放射性危害的其他工业废渣材料,但必须经过现场试验证明其经济技术效果良好且施工措施完善后方可使用。

2-2 GB50290—2014土工合成材料应用技术规范附条文
土工合成材料加筋垫层所选用土工合成材料的品种与性能及填料,应根据工程特性和地基土质条件,按照现行国家标准《土工合成材料应用技术规范》(GB/T50290—2014)的要求,通过设计计算并进行现场试验后确定。土工合成材料应采用抗拉强度较高、耐久性好、抗腐蚀的土工带、土工格栅、土工格室、土工垫或土工织物等土工合成材料;垫层填料宜用碎石、角砾、砾砂、粗砂、中砂等材料,且不宜含氯化钙、碳酸钠、硫化物等化学物质。当工程要求垫层具有排水功能时,垫层材料应具有良好的透水性。在软土地基上使用加筋垫层时,应保证建筑物稳定并满足允许变形的要求。
2.施工技术要点
(1)铺设垫层前应验槽,将基地表面的浮土、淤泥、杂物等清理干净,两侧应设一定坡度,防止振捣时塌方。当垫层底部存在古井、古墓、洞穴、旧基础、暗塘等软硬不均的部位时,应根据建筑对不均匀沉降的要求予以处理,并经检验合格后,方可铺填垫层。
(2)垫层底面宜设在同一标高上,如深度不同,基坑底土面应挖成阶梯或斜坡搭接,并按先深后浅的顺序进行垫层施工,搭接处应夯压密实。分层铺实时,接头应做成斜坡或阶梯搭接,每层错开0.5~1.0m,并注意充分捣实。
(3)人工级配的砂石材料,施工前应充分拌匀,再铺夯压实。
(4)垫层施工应根据不同的换填材料选择施工机械。粉质黏土、灰土宜采用平碾、振动碾或羊足碾,以及蛙式夯、柴油夯。砂石垫层等宜用振动碾。粉煤灰垫层宜采用平碾、振动碾、平板振动器、蛙式夯。矿渣垫层宜采用平板振动器或平碾,也可采用振动碾。
(5)垫层的施工方法、分层铺填厚度、每层压实遍数等宜通过试验确定。除接触下卧软土层的垫层底部应根据施工机械设备及下卧层土质条件确定厚度外,一般情况下,垫层的分层铺填厚度可取200~300mm。分层厚度可用样桩控制。在施工时,当下层的密实度经检验合格后,方可进行上一层施工。为了保证分层压实质量,应控制机械碾压速度。
(6)基坑开挖时应避免坑底土层受扰动,可保留180~200mm厚的土层暂不挖去,待铺填垫层前再由人工挖至设计标高。严禁扰动垫层下的软弱土层,应防止软弱土层被践踏、受冻或受水浸泡。在碎石或卵石垫层底部宜设置150~300mm厚的砂垫层或铺一层土工织物,以防止软弱土层表面的局部破坏,同时必须防止基坑边坡塌土混入垫层。
(7)换填垫层施工应注意基坑排水,除采用水撼法施工砂垫层外,不得在浸水条件下施工,必要时应采取降低地下水位的措施。要注意边坡稳定,以防止塌土混入砂石垫层中影响其质量。
(8)当采用水撼法或插振法施工时,应在基槽两侧设置样桩,控制铺砂厚度,每层为250mm。铺砂后,灌水与砂面齐平,以振动棒插入振捣,依次振实,以不再冒气泡为准,直至完成。垫层接头应重复振捣,插入式振动棒振完所留孔洞后应用砂填实。在振动首层垫层时,不得将振动棒插入原土层或基槽边部,以避免使软土混入砂垫层而降低砂垫层的强度。
(9)垫层铺设完毕后,应及时回填,并及时对基础进行施工。
(10)冬季施工时,砂石材料中不得夹有冰块,并应采取措施防止砂石内水分冻结。
(11)粉质黏土、灰土垫层及粉煤灰垫层施工应符合下列规定:
①粉质黏土及灰土垫层分段施工时,不得在柱基、墙角及承重窗间墙下接缝。
②上下两层的缝距不得小于500mm,接缝处应夯压密实。
③灰土拌和均匀后,应当日铺填夯压;灰土夯压密实后,3天内不得受水浸泡。
④粉煤灰垫层铺填后,宜当天压实,每层验收后应及时铺填上层或封层,并应禁止车辆碾压通行。
⑤垫层竣工验收合格后,应及时进行基础施工与基坑回填。
(12)土工合成材料施工(见图2-2),应符合以下要求:

图2-2 土工合成材料垫层
①下铺地基土层顶面应平整。
②土工合成材料铺设顺序应先纵向后横向,且应把土工合成材料张拉平整、绷紧,严禁有折皱。
③土工合成材料的连接宜采用搭接法、缝接法或胶接法,连接强度不应低于原材料抗拉强度,端部应采用有效固定方法,防止筋材拉出。
④应避免土工合成材料暴晒或裸露,阳光暴晒时间不应大于8h。
3.质量控制及质量检验
(1)施工前应检查原材料,如灰土的土料、石灰以及配合比、灰土拌匀程度。
(2)施工中应检查分层铺设厚度,分段施工时上下两层的搭接长度,夯实时加水量、压实遍数,等。
(3)换填垫层的施工质量检验应分层进行,并应在每层的压实系数符合设计要求后铺填上层。垫层的压实标准参见表2-2。
表2-2 各种垫层的压实标准

注:(1)压实系数λc为土的控制干密度ρd与最大干密度ρdmax的比值;土的最大干密度宜采用击实试验确定,碎石或卵石的最大干密度可取2.1~2.2t/m3;
(2)表中压实系数λc系使用轻型击实试验测定土的最大干密度ρdmax时给出的压实控制标准,采用重型击实试验时,对粉质黏土、灰土、粉煤灰及其他材料压实标准应为压实系数λc≥0.94。
(4)对粉质黏土、灰土、砂石、粉煤灰垫层的施工质量检验可选用环刀取样、静力触探、轻型动力触探或标准贯入试验等方法进行检验;对碎石、矿渣垫层可用重型动力触探等进行检验。压实系数可采用灌砂法、灌水法或其他方法进行检验。
(5)采用环刀法检验垫层的施工质量时,取样点应选择位于每层厚度的2/3深度处。检验点数量,条形基础下垫层每10~20m2不应少于1个点,独立基础、单个基础下垫层不应少于1个点,其他基础下垫层每50~100m2不应少于1个点。采用标准贯入试验或动力触探检验垫层的施工质量时,每分层检验点的间距不应大于4m。
(6)竣工验收采用静载荷试验检验垫层承载力,且每个单体工程不宜少于3点;对于大型工程应按单体工程的数量或工程划分的面积确定检验点数。
(7)对加筋垫层中土工合成材料的检验应符合下列要求:
①土工合成材料质量应符合设计要求、外观无破损、无老化、无污染。
②土工合成材料应可张拉、无折皱、紧贴下承层,锚固端应锚固牢固。
③上下层土工合成材料搭接缝应交替错开,搭接强度应满足设计要求。
2.1.3 强夯法
强夯法是反复将夯锤提到高处使其自由落下,给地基以冲击和振动能量,将地基土夯实的地基处理方法,属于夯实地基方法的一种。重复夯打击实地基,使地基形成了一层比较密实的硬壳层,从而提高了地基的强度。强夯法适用于处理碎石土、沙土、低饱和度的粉土和黏性土、湿陷性黄土、素填土和杂填土等地基;适用于处理大面积填土地基。强夯机械如图2-3所示。

图2-3 强夯机械
1.施工前准备
(1)作业条件
①施工场地要做到“三通一平”,即场地的地上电线、线下管网和其他障碍物应得到清理或妥善安置,施工用的临时设施要准备就绪。
②施工现场周围的建筑、构筑物(含文物保护建筑)、古树、名木和地下管线要得到可靠的保护。当强夯能量有可能对邻近建筑物产生影响时,应在施工区边界开挖隔震沟。隔震沟的规模应根据影响程度而定。
③应具备详细的岩土工程地质及水文地质勘查资料,拟建建筑物平面位置图、基础平面图、剖面图,强夯地基处理施工图及工程施工组织设计。
④施工放线。依据甲方提供的建筑物控制点坐标、水准点高程及书面资料,进行施工放线、放点,放线应将强夯处理范围白灰线画出来,对建筑物控制点埋设木桩。将施工测量控制点引至不受施工影响的稳固地点。必要时,对建筑物控制点坐标和水准点高程进行验测,要求使用的测量仪器经过鉴定合格。
⑤设备安装及调试。起吊设备进场后应及时安装及调试,保证吊车行走、运转正常;起吊滑轮组与钢丝绳连接紧固,安全可靠,起吊挂钩锁定装置应牢固可靠,脱钩自由灵敏,与钢丝绳连接牢固;夯锤重量、直径、高度应满足设计要求,夯锤挂钩与夯锤整体应连接牢固;施工用推土机应运转正常。
(2)机具准备
①夯锤。10~40t,铸钢或钢筒混凝土制作,宜优先选用铸钢夯锤。底面形式宜用圆形,锤的底面宜均匀设置若干个与其顶面贯通的排气孔,孔径可取250~300mm。锤底静接地压力值可取25k~40kPa。
②起重机。20~50t履带式起重机或汽车起重机,宜优先选用履带式起重机。起吊能力为锤重的1.5~2.0倍。
③脱钩装置。国内目前使用较多的是通过动滑轮组用脱钩装置来起落夯锤。脱钩装置要求有足够的强度,使用灵活,脱钩快速安全。
④推土机。TS140、TS220、D80等,要满足现场推土需要。
(3)单点夯试验
①在施工场地附近或场地内,选择具有代表性的适当位置进行单点夯试验。试验点数量根据工程需要确定,一般不少于2点。
②根据夯锤直径,用白灰画出试验中心点位置及夯击圆界限。
③在夯击试验点界限外两侧,以试验中心点为原点,对称等间距埋设标高施测基准桩,基准桩埋设在同一直线上,直线通过试验中心点,基准桩间距一般为1m,基准桩埋设数量视单点夯影响范围而定。
④在远离试验点(夯击影响区外)处架设水准仪,进行各观测点的水准测量,并做记录。
⑤平稳起吊夯锤至设计要求的夯击高度,释放夯锤使其自由平稳落下。
⑥用水准仪对基准桩及夯锤顶部进行水准高程测量,并做好试验记录。
⑦重复以上⑤⑥两步骤至试验要求的夯击次数。
2.施工工艺及注意事项
(1)施工工艺流程
①清理并平整施工场地。
②铺设垫层。在地表形成硬层,用以支承起重设备,确保机械通行和施工,同时可加大地下水和表层面的距离,防止降低夯击的效率。
③标出第一遍夯击点的位置,并测量场地高程。
④起重机就位,使夯锤对准夯点位置。
⑤测量夯前锤定标高。
⑥将夯锤起吊到预定高度,待夯锤脱钩自由下落后放下吊钩,测量锤顶高程;若发现坑底倾斜而造成夯锤歪斜时,应及时将底坑整平。
⑦重复⑥,按设计规定的夯击次数及控制标准,完成一个夯点夯击。
⑧重复④~⑦,完成全部夯点的第一遍夯击。
⑨用推土机将夯坑填平,并测量场地高程。
⑩在规定间隔时间后,通过上述步骤逐次完成全部夯击遍数,最后用最低能量满夯,将场地表层土夯实,并测量场地高程。
(2)施工注意事项

图2-4 强夯顺序
①强夯前应做好夯区地质勘查,对不均匀土层适当增多钻孔和原位测试工作,掌握土质情况,作为制定强夯方案和对比夯前、夯后的加固效果的依据,必要时进行现场试验性强夯,确定强夯施工的各项参数。
②强夯应分段进行,顺序从边缘向中央(见图2-4)。对厂房柱基亦可一排一排夯,起重机直线行驶,从一边向另一边进行,每夯完一遍,用推土机整平场地,放线定位即可进行下一遍夯击。强夯法的加固顺序是:先深后浅,即先加固深土层,再加固中土层,最后加固表土层。当最后1遍夯完后,再以低能量满夯2遍,如有条件,宜采用小锤夯击。
③严格遵守强夯施工程序及要求,做到夯锤升降平衡,对准夯坑,避免歪夯,禁止错位夯击施工,一旦发现歪夯,应立即采取纠正措施。
④夯锤的通气孔在施工时应保持畅通,如被堵塞,应立即疏通,以防产生“气垫”效应,影响强夯施工质量。
⑤不同遍数施工之间需要控制的施工间隔时间应根据地质条件、地下水条件、气候条件等因素由设计人员提出,一般宜为3~7d。
⑥施工过程中避免夯坑内积水。一旦积水要及时排除,必要时换土再夯,避免“橡皮土”出现。
⑦冬、雨季施工:
a.雨季施工。应做好气象信息收集工作;夯坑应及时回填夯平,避免坑内积水渗入地下影响强夯效果;夯坑内一旦积水,应及时排出;场地因降水浸泡,应增加消散期,严重时可采用换土再夯等措施。
b.冬季施工。表层冻土较薄时,此因素不予考虑,正常施工;当冻土较厚时应首先将冻土击碎或将冻层挖除,然后再按各点规定的夯击数施工。在第一遍及第二遍夯完整平后宜在5d后进行下一遍施工。
⑧做好施工过程的监测和记录工作,包括检查夯锤重和落距,对夯点放线进行复核,检查夯坑位置,按要求检查每个夯点的夯击次数和每击的夯沉量等,并对各项参数及施工情况进行详细记录,作为质量控制的依据。
⑨安全措施:
a.在起夯时,吊车正前方、吊臂下和夯锤下严禁站人,需要整平夯坑内土方时,要先将夯锤吊离并放在坑外地面后方可下人。
b.施工人员进入现场要戴安全帽,夯击时要保持离夯坑10m以上距离。
c.六级以上大风天气,以及雨、雾、雪、风沙扬尘等能见度低时暂停施工。
3.质量检验标准
(1)检查施工过程中的各项测试数据和施工记录,不符合设计要求时应补夯或采取其他有效措施。施工前应检查夯锤重量、尺寸,落距控制手段,排水设施及被夯地基的土质。施工中应检查落距、夯击遍数、夯点位置、夯击范围。
(2)强夯处理后的地基竣工验收承载力检验,应在施工结束后间隔一定时间方能进行。对于碎石土和砂土地基,其间隔时间可取7~14d;粉土和黏性土地基可取14~28d。强夯置换地基间隔时间可取28d。
(3)强夯地基质量检验标准应符合表2-3的规定。
表2-3 强夯地基质量检验标准

2.1.4 灰土挤密桩和土挤密桩复合地基
灰土挤密桩和土挤密桩复合地基利用成孔过程中的横向挤压作用,桩孔内土被挤向周围,使桩间土挤密,然后将灰土或素土分层填入桩孔内,并分层夯填密实至设计标高。前者称为灰土挤密桩法,后者称为土挤密桩法。夯填密实的灰土挤密桩或土挤密桩,与挤密的桩间土形成复合地基。上部荷载由桩体和桩间土共同承担。对土挤密桩法而言,若桩体和桩间土密实度相同时,形成均质地基。灰土挤密桩如图2-5所示。

图2-5 灰土挤密桩
灰土挤密桩法和土挤密桩法适用于处理地下水位以上的湿陷性黄土、素填土、杂填土等地基,不适宜在地下水位以下使用,可处理的地基深度为5~15m。当以消除地基的湿陷性为主要目的时,宜采用土挤密桩法;当以提高地基土的承载力或增强其水稳性为主要目的时,宜采用灰土挤密桩法。
1.施工前准备
(1)桩的构造和布置
①桩孔直径。根据工程量、挤密效果、施工设备、成孔方法及经济等情况而定,一般选用300~600mm。
②桩长。根据土质情况、桩处理地基的深度、工程要求和成孔设备等因素确定,一般为5~15m。
③桩距和排距。桩孔一般按等边三角形布置,其间距和排距由设计确定。
④处理宽度。处理地基的宽度一般大于基础的宽度,由设计确定。
⑤地基的承载力和压缩模量。灰土挤密桩处理地基的承载力标准值,应由设计通过原位测试或结合当地施工经验确定。灰土挤密桩地基的压缩模量应通过试验或结合本地经验确定。
(2)机具设备及材料要求
①成孔设备。一般采用0.6或1.2t柴油打桩机或自制锤击式打桩机,亦可采用冲击钻机。
②夯实机具。常用夯实机具有偏心轮夹杆式夯实机和卷扬机提升式夯实机两种,后者工程中应用较多。夯锤用铸钢制成,重量一般选用100~300kg,其竖向投影面积的静压力不小于20kPa。夯锤最大部分的直径应较桩孔直径小100~150mm,以便填料顺利通过夯锤4周。夯锤形状下端应为抛物线形锥体或尖锥形锥体,上段成弧形。
③桩孔内的填料。桩孔内的灰土填料,其消石灰和土的体积配合比,宜为2∶8或3∶7。土料宜选用粉质黏土,土料中的有机质含量不应超过5%,且不得含有冻土,渣土垃圾颗粒直径不应超过15mm。石灰可选用新鲜的消石灰或生石灰粉,粒径不应大于5mm。孔内填料应分层回填夯实,填料的平均压实系数λc不应低于0.97,其中压实系数最小值不应低于0.93。
2.施工工艺方法要点
(1)工艺流程
灰土挤密桩工艺流程如图2-6所示。

图2-6 灰土挤密桩工艺流程
(2)方法要点
①施工前应在现场进行成孔、夯填工艺和挤密效果试验,以确定分层填料厚度、夯击次数和夯实后干密度等要求。
②桩施工一般采取先将基坑挖好,预留200~300mm厚的土层,然后在坑内施工灰土桩。桩的成孔方法可根据现场机具条件选用沉管(振动、锤击)法、爆扩法、冲击法或洛阳铲成孔法等。沉管法是用打桩机将与桩孔同直径的钢管打入土中,使土向孔的周围挤密,然后缓慢拔管成孔。桩管顶设桩帽,下端做成锥形约成60°角,桩尖可以上下活动,以利空气流动,可减少拔管时的阻力,避免塌孔。成孔后应及时拔出桩管,不应在土中搁置时间过长。成孔施工时,地基土宜接近最优含水量,当含水量低于12%时,宜加水增湿至最优含水量。本法简单易行,孔壁光滑平整,挤密效果好,应用最广。但沉管法处理深度受桩架限制,一般不超过8m。爆扩法是用钢钎打入土中形成直径25~40mm孔或用洛阳铲打成直径为60~80mm孔,然后在孔中装入条形炸药卷和2~3个雷管,爆扩成直径20~45mm孔。本法工艺简单,但孔径不易控制。冲击法是使用冲击钻钻孔,将0.6~2.2t重锥形锤头提升0.5~2.0m高后落下,反复冲击成孔,并用泥浆护壁,直径可达500~600mm,深度可达15m以上,适于处理湿陷性较大的土层。
③桩的施工顺序应先外排后里排,同排内应间隔1~2孔进行;对大型工程可采取分段施工,以免因振动挤压造成相邻孔缩孔或塌孔。成孔后应清底夯实、夯平,夯实次数不少于8次,并立即夯填灰土。
④桩孔应分层回填夯实,每次回填厚度为250~400mm,人工夯实用重25kg、带长柄的混凝土锤,机械夯实用偏心轮夹杆式夯实机或卷扬机提升式夯实机,或链条传动摩擦轮提升连续式夯实机,一般落锤高度不小于2m,每层夯实不少于10锤。施打时,逐层以量斗定量向孔内下料,逐层夯实。当采用连续夯实机时,则将灰土用铁锹不间断地下料,每下2锹夯2击,均匀地向桩孔下料、夯实。桩顶应高出设计标高15cm,挖土时再将高出部分铲除。
⑤若孔底出现饱和软弱土层时,可加大成孔间距,以防由于振动而造成已打好的桩孔内挤塞;当孔底有地下水流入时,可采用井点降水后再回填填料或向桩孔内填入一定数量的干砖渣和石灰,经夯实后再分层填入填料。
3.质量控制
(1)施工前应对土及灰土的质量、桩孔放样位置等进行检查。
(2)施工中应对桩孔直径、桩孔深度、夯击次数、填料的含水量等进行检查。
(3)施工结束后应对成桩的质量及地基承载力进行检验。
(4)灰土挤密桩地基质量检验标准如表2-4所示。
表2-4 灰土挤密桩地基质量检验标准

2.1.5 水泥土搅拌桩复合地基
水泥土搅拌桩复合地基是指利用水泥(或水泥系材料)为固化剂,通过特制的搅拌机械,在地基深处对原状土和水泥进行强制搅拌,形成水泥土圆柱体,与原地基土构成地基(见图2-7)。水泥土搅拌桩除作为竖向承载的复合地基外,还可以用于基坑工程围护挡墙、被动区加固、防渗帷幕等。加固体形状可分为柱状、壁状、格栅状或块状等。水泥土搅拌桩根据固化剂掺入状态的不同,分为湿法(浆液搅拌)和干法(粉体喷射搅拌)。

图2-7 水泥土搅拌桩复合地基
水泥土搅拌桩适用于处理正常固结的淤泥与淤泥质土、粉土、饱和黄土、素填土、黏性土以及无流动地下水的饱和松散砂土等地基。当地基土的天然含水量小于30%(黄土含水量小于25%)、大于70%或地下水的pH值小于4时不宜采用干法。
1.施工设备
水泥土搅拌桩的主要施工设备为深层搅拌机,有中心管喷浆方式的SJB-1型搅拌机和叶片喷浆方式的GZB-600型搅拌机两类。
2.施工工艺流程
水泥土搅拌桩复合地基施工工艺流程如下(见图2-8):

图2-8 水泥土搅拌桩复合地基施工工艺流程
(1)施工现场事先应予以平整,必须清除地上和地下的障碍物。遇到明浜、池塘及洼地时应抽水和清淤,回填土料应压实,不得回填生活垃圾。
(2)在制定水泥土搅拌施工方案前,应做水泥土的配比试验。根据测定的各水泥土的不同龄期,不同水泥土配比试块的强度,确定施工时的水泥土配比。
(3)水泥土搅拌桩施工前应根据设计进行工艺性试桩,数量不得少于3根,多头搅拌不得少于3组,从而确定水泥土搅拌施工参数及工艺,以及水泥浆的水灰比、喷浆压力、喷浆量、旋喷速度、提升速度、搅拌次数等。
(4)搅拌机械就位、调平,为保证桩位准确使用定位卡,桩位对中偏差应不大于20mm,导向架和搅拌轴应与地面垂直,垂直度的偏差不大于1.5%。
(5)预搅下沉至设计加固深度后,边喷浆(粉)边搅拌提升至预定的停浆(灰)面。
(6)重复钻进搅拌,按前述操作要求进行,如喷粉量或喷浆量已达到设计要求时,只需复搅不再送粉或只需复搅不再送浆。
(7)根据设计要求,喷浆(粉)或仅搅拌提升至预定的停浆(灰)面时,关闭搅拌机械。
(8)在预(复)搅下沉时,也可采用喷浆(粉)的施工工艺,但必须确保全桩长上下至少再重复搅拌一次。
(9)对地基土进行干法咬合加固时,如复搅困难,可采用慢速搅拌,保证搅拌的均匀性。
3.施工注意事项
(1)湿法施工控制要点:
①水泥浆液到达喷浆口的出口压力不应小于10MPa。
②施工前应确定灰浆泵输浆量、灰浆经输浆管到达搅拌机喷浆口的时间和起吊设备提升速度等施工参数,并根据设计要求通过工艺性成桩试验确定施工工艺。
③使用水泥都应过筛,制备好的浆液不得离析,泵送必须连续。拌制水泥浆液的罐数、水泥和外掺剂用量以及泵送浆液的时间等应有专人记录;喷浆量及搅拌深度必须采用经国家计量部门认证的检测仪器进行自动记录。
④搅拌机喷浆提升的速度和次数必须符合施工工艺的要求,并应有专人记录。
⑤当水泥浆液到达出浆口后,应喷浆搅拌30s,在水泥浆与桩端土充分搅拌后,再开始提升搅拌头。
⑥搅拌机预搅下沉时不宜冲水,当遇到硬土层下沉太慢时,方可适量冲水,但应考虑冲水对桩身强度的影响。
⑦施工时如因故停浆,应将搅拌头下沉至停浆点以下0.5m处,待恢复供浆时再喷浆搅拌提升。若停机超过3h,宜先拆卸输浆管路,并妥加清洗。
⑧壁状加固时,相邻桩的施工时间间隔不宜超过24h。若间隔时间太长,与相邻桩无法搭接时,应采取局部补桩或注浆等补强措施。
⑨喷浆未到设计桩顶标高(或底部桩端标高),而集料斗中浆液已排空时,应检查投料量、有无漏浆、灰浆泵输送浆液流量。其处理方法为:重新标定投料量,或检修设备,或重新标定灰浆泵输送流量。
⑩喷浆到设计桩顶标高(或底部桩端标高),而集料斗中浆液剩浆过多时,应检查投料量、输浆管路部分是否堵塞、灰浆泵输送浆液流量。其处理方法为:重新标定投料量,或清洗输浆管路,或重新标定灰浆泵输送流量。
(2)干法施工控制要点:
①喷粉施工前应仔细检查搅拌机械、供粉泵、送气(粉)管路、接头和阀门的密封性、可靠性。送气(粉)管路的长度不宜大于60m。
②水泥土搅拌法(干法)喷粉施工机械必须配置经国家计量部门确认的具有能瞬时检测并记录粉体计量的装置及搅拌深度的自动记录仪。
③搅拌头每旋转一周,其提升高度不得超过16m。
④搅拌头的直径应定期复核检查,其磨耗量不得大于10mm。
⑤当搅拌头到达设计桩底以上1.5m时,应立即开启喷粉机提前进行喷粉作业。当搅拌头提升至地面下500mm时,喷粉机应停止喷粉。
⑥成桩过程中因故停止喷粉,应将搅拌头下沉至停灰面以下1m处,待恢复喷粉时再喷粉搅拌提升。
(3)搅拌机预搅下沉不到设计深度,但电流不高,可能是土质黏性大,搅拌机自重不够造成的。应采取增加搅拌机自重或开动加压装置。
(4)搅拌钻头与混合土同步旋转,是灰浆浓度过大或搅拌叶片角度不适宜造成的。可采取重新确定浆液的水灰比,或者调整叶片角度、更换钻头等措施。
4.质量检验与验收
(1)施工期质量检验
施工期质量检验包括以下内容:
①水泥土搅拌施工时,应随时检查施工中的各项记录,如发现地质条件发生变化,或有遗漏,或水泥土搅拌桩(水泥土搅拌点)施工质量不符合规定要求,应进行补桩或采取其他有效的补救措施。
②重点检查输浆量(水泥用量)、输浆速度、总输浆时间、桩长、搅拌头转速和提升速度、复搅次数和复搅深度、停浆处理方法等。
(2)竣工后质量验收
竣工后质量验收应包括以下内容:
①水泥土搅拌施工结束28天后进行检验。
②水泥土搅拌桩桩体的主要检测内容如下:
a.成桩后3天内,可用轻型动力触探(N10)检查上部桩身的均匀性。检查量为施工总桩数的1%,且不少于3根。
b.成桩7天后,采用浅部开挖桩头的方法进行检查,开挖深度宜超过停浆(灰)面下0.5m,目测检查搅拌的均匀性,量测成桩直径。检查量为总桩数的5%。
c.桩身强度检测应在成桩28天后,用双管单动取样器钻取芯样作搅拌均匀性和水泥土抗压强度检验。检验量为施工总桩(组)数的0.5%,且不少于6点。钻芯有困难时,可采用单桩抗压静载荷试验检验桩身质量。
③承载力检测。竖向承载水泥土搅拌桩复合地基竣工验收时,承载力检验应采用复合地基载荷试验和单桩载荷试验。载荷试验必须在桩身强度满足试验荷载条件时进行,并宜在成桩28天后进行。验收检测检验数量为桩总数的0.5%~1%,其中单项工程单桩复合地基载荷试验的数量不应少于3根(多头搅拌为3组),其余可进行单桩静载荷试验或单桩、多桩复合地基载荷试验。
④基槽开挖后,应检验桩位、桩数与桩顶质量,如不符合设计要求,应采取有效补救措施。
(3)检验与验收标准
水泥土搅拌桩复合地基的质量检验内容及标准应符合表2-5的要求。
表2-5 水泥土搅拌桩复合地基质量检验内容及标准

2.1.6 地基局部处理
地基的局部处理,常见于施工验槽时查出或出现的局部与设计要求不符的地基,如槽底倾斜,墓坑,暖气沟或电缆等穿越基槽,古井,大块孤石等。地基处理时应根据不同情况妥善处理。处理的原则是使地基不均匀沉降减少至允许范围之内。下面就常见形式做一简单介绍。
1.局部软土地基处理
(1)基坑、松土坑的处理
①坑的范围较小时,可将坑中虚土全部挖出,直至见到老土为止,然后用与老土压缩性相近的土回填,分层夯实至基底设计标高。若地下水位较高或坑内积水无法夯实时,可用砂、石分层夯实回填。
②坑的范围较大时,可将该范围内的基槽适当加宽,再回填土料,方法及要求同上。
③坑较深、挖除全部虚土有困难时,可部分挖除,挖除深度一般为基槽宽的2倍。剩余虚土为软土时,可先用块石夯实挤密后再回填。也可采用加强基础刚度、用梁板形式跨越、改变基础类或采用桩基进行处理。
(2)“橡皮土”的处理
当地基为含水量很大、趋于饱和的黏性土时,反复夯打后会使地基变成所谓的“橡皮土”。因此,当地基为含水量很大的黏性土时,应先采用晾槽或掺生石灰的方法减小土的含水量,然后再根据具体情况选择施工方法及基础类型。
如果地基已产生了“橡皮土”的现象,则应采取如下措施:
①把“橡皮土”全部挖除干净,然后再回填好土至设计标高。
②若不能把“橡皮土”完全清除干净,则利用碎石或卵石打入,将泥挤紧,或铺撒吸水材料(如干土、碎砖、生石灰等)。
③若在施工中扰动了基底土,对于湿度不大的土,可做表面夯实处理。对于软黏土,则需掺入砂、碎石或碎砖才能夯打,或将扰动土全部清除,另填好土夯实。
(3)管道穿越基槽的处理
①槽底有管道时,最好是能拆迁管道,或将基础局部加深,使管道从基础之上通过。
②如果管道必须埋于基础之下,则应采取保护措施,避免将管道压坏。
③若管道在槽底以上穿过基础或基础墙时,应采取防漏措施,以免漏水浸湿地基造成不均匀下沉。当地基为填土或湿陷性土时,尤其应注意。另外,有管道通过的基础或基础墙,必须在管道的周围预留足够尺寸的孔洞。在管道上部预留的空隙应大于房屋预估的沉降量,以保证管道的安全。
2.局部坚硬地基处理
(1)砖井、土井的处理
①井位于基槽的中部。若井的进口填土较密实时,可将井的砖圈拆去1m以上,用2∶8或3∶7灰土回填,分层夯实至槽底;若井的直径大于1.5m,可将土井挖至地下水面,每层铺20cm粗骨料,分层夯实至槽底整平,上面做钢筋混凝土梁(板)跨越它们。
②井位于基础的转角处。除采用上述的回填办法外,还可视基础压在井口的面积大小,采用从两端墙基中伸出挑梁,或将基础沿墙长方向向外延长出去,跨越井的范围,然后再在基础墙内采用配筋或加钢筋混凝土梁(板)来加强。
(2)基岩、旧墙基、孤石的处理
当基槽下发现有部分比其邻近地基土坚硬得多的土质时(如槽下遇到基岩、旧墙基、大树根和压实的路面、老灰土等)均应尽量挖除,然后填与地基土质相近的较软弱土,挖除厚度视大部分地基土层的性质而定,一般为1m左右。
如果局部硬物不易挖除时应考虑加强上部刚度。如果在基础墙内加钢筋或钢筋混凝土梁等,尽量减少可能产生的不均匀沉降对建筑物造成的伤害。
(3)防空洞的处理
①防空洞砌筑质量较好,有保留价值时,可采用承重法:
a.如果洞顶施工质量不好,可拆除重做素混凝土拱顶或钢筋混凝土拱顶,也可在原砖砌拱顶上现浇钢筋混凝土拱,使砖、混凝土共同组成复合承重的拱顶。
b.如果洞顶质量较好,但承重强度不足,可沿洞壁浇筑钢筋混凝土扶壁柱,并与拱顶浇为一体。
②当防空洞埋置深度不大,靠近建筑物且又无法避开时,可适当加深基础,使基础埋深与防空洞取平。
③如果防空洞较深,其拱顶层距地面深达6~7m,拱顶距基底也有4~5m之多,防空洞本身质量亦较好时,防空洞可以不加处理,但要加强上部结构整体刚度,防止出现裂缝,或因地基承载不均匀,导致产生不均匀沉降。
④建筑物所在位置恰遇防空洞,为避开防空洞时,可作以下处理:
a.采用建筑物移位法,即首先考虑建筑物适当移位,这样既可保留防空洞,建筑物地基又不用处理。
b.如果受建筑物限制不能移位,就考虑建筑物某道或某几道承重墙是否可错开防空洞,使承重墙不直接压在防空洞上。
c.建筑物因地制宜、“见缝插针”。根据现有能避开防空洞的场地,将建筑物平面做成点式、L形、U形等。