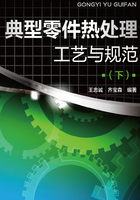
第2章 金属切削机床典型零件的热处理工艺与规范
2.1 概述
金属切削机床是采用切削的方法把金属毛坯加工成机器零件的机器,它是制造机器的机器,故又称“工作母机”,简称机床。在现代机械制造工业中,机床在各类机器制造装备中所占比重较大,一般都在50%以上,所担负的工作量占机器总制造工作量的40%~60%,对于具有一定形状、尺寸和表面质量要求的金属零件,特别是精密零件的加工,主要是在金属切削机床上完成的。一个国家机床的拥有量、产量、品种和质量如何,是衡量其工业水平的标志之一。
金属切削机床必须具有较高的精度和精度保持性。金属切削机床的精度主要取决于关键零件的制造精度和装配精度。而这些零件的强度、粗糙度、耐磨性及尺寸稳定性等性能又直接与热处理工艺密切相关。因此,机床零件的热处理在机床制造业中占有举足轻重的地位。
随着现代科学技术的迅猛发展,高速自动化切削机床、数控切削机床、高精度精密切削机床、重型数控机床及加工中心等发展很快。金属切削机床的工作载荷加重、运动速度更快,机械零件的精度要求则更高。因此,对机床零件材料与热处理提出了更高、更全面、更严格的要求。
2.1.1 金属切削机床零件热处理的特点
我国机床行业,中小型机床一般为批量化生产;大型及重型机床为单个或小批量生产。一般机床的工作条件如承载、受冲击及润滑条件等都明显优于汽车、拖拉机及重型机械,但其对零件的精度和精度保持性要求较高。故机床零件的热处理特点可归结为如下6点。
(1)用钢简单
一般采用非合金(碳素)结构钢及低合金结构钢。少数零件,如镶钢导轨、淬硬丝杠等采用低合金工具钢及轴承钢等。
(2)采用周期式作业炉
大部分零件的无氧化加热采用盐浴炉、真空炉或在气体渗碳炉中滴注煤油生成保护气氛中进行。
(3)局部淬硬及表面淬硬零件较多
有许多机床零件只要求局部表面有高的耐磨性,除少数零件采用盐浴炉局部淬硬外,大部分零件采用局部表面淬火法(如感应加热、激光加热、超音频加热等)淬硬。
(4)精密零件要求具有高的尺寸稳定性
通常在工序中常安排有一次或多次稳定化处理,如去应力退火、低温时效处理及冷处理等,尽量减少残余内应力,以保证高的尺寸稳定性。
(5)广泛采用低温化学热处理
机床零件的设计多数从刚性考虑,对热处理主要要求变形小,耐磨性高,尺寸稳定性好。因此渗氮、氮碳共渗等低温化学热处理工艺获得广泛应用。
(6)大部分钢制零件必须经过预先热处理
如铸钢件、锻件及轧材等,必须经过退火、正火或调质处理等预先热处理,以提高其强度,消除组织缺陷及改善加工工艺性能;同时也为最终热处理做好组织准备,减少热处理变形。
2.1.2 机床零件常用的热处理工艺
2.1.2.1 预备热处理工艺
一般在锻造或粗机械加工后进行,常用的有以下几种。
(1)退火
各种退火工艺特点如表2-1所示。
表2-1 退火和正火热处理特点

(2)正火
正火与退火的主要区别在于冷却速度不同,正火冷却速度较快,得到的组织较细,硬度、强度、韧性等也较高。当碳钢中C<0.6%时,正火后的组织为F+S;当C=0.6%~1.4%时,正火后组织为S(伪共析组织)。
(3)调质处理
零件经机械加工后,加热淬火,然后于500~650℃下高温回火,获得均匀的回火索氏体的热处理工艺称为调质处理。其目的在于使零件获得良好的综合力学性能。
同时,调质处理也为最终热处理做好显微组织准备。这是因为,若淬火前材料的组织为经调质处理获得的回火索氏体,其淬火温度可降低,奥氏体化时间可减少,故可减少淬火变形。对淬火易变形的零件,制定工艺时往往要增加调质工序。
2.1.2.2 最终热处理工艺
一般在半精机械加工,甚至可在精机械加工后进行。常用的有以下几种。
(1)淬火与回火
将工件加热至临界点(Ac3或Ac1)以上,保温后以大于(上)临界冷却速度的速度快速冷却,使奥氏体转变为马氏体(或下贝氏体)的热处理工艺称为淬火;而回火则指将淬火后的钢加热至A1以下的某一温度后进行冷却的热处理工艺。
一般淬火工件必须经过回火后方能使用。淬火与回火总是经常配合使用的两种应用最广且最重要的热处理工艺。
淬火的目的就是为了获得马氏体(或下贝氏体)组织,以提高钢件的力学性能。而淬火钢件回火的目的在于以下几点。
①降低脆性,减少或消除内应力,防止工件变形开裂。
②调整淬火钢的组织与性能,用不同的回火温度配合,获得工件使用要求的性能。
③稳定工件尺寸,以保证工件在使用过程中不发生尺寸和形状变化。
④对于某些高淬透性的合金钢,空冷便可淬成马氏体,如采用退火软化,则周期很长。此时可采用高温回火,使碳化物聚集长大,降低硬度,以利切削加工,同时可缩短软化周期。
⑤对于有色金属合金、奥氏体不锈钢等,淬火即固溶处理。
应当说明,对于未淬火的钢,回火一般是没有意义的,但淬火钢不经回火一般也不能直接使用。为了避免工件在放置过程发生变形和开裂,淬火后应及时进行回火。
根据淬火加热温度的不同,即奥氏体化的程度不同,淬火可分为完全淬火和不完全淬火。
完全淬火 亚共析钢加热至Ac3以上30~50℃,共析钢加热至Ac1以上30~50℃,保温后快速冷却。
不完全淬火 过共析钢加热至Ac1以上30~50℃,保温后快速冷却,渗碳体未全部溶于奥氏体而保存下来。亚共析钢在特殊情况下,也采用不完全淬火(即亚温淬火),这时铁素体未全部溶于奥氏体淬火冷却后被保存下来,起一定的软垫作用,它适用于在低温下工作的零件及某些零件易于开裂部位的淬火等场合。
同样,根据回火温度的不同,可分为低温回火、中温回火和高温回火,其特征如表2-2所示。淬火+高温回火获得回火索氏体组织的热处理工艺即为调质处理。
表2-2 回火组织及性能特点

(2)表面强化热处理
把零件表面(全部或局部)加热和冷却来改变零件表面性能的热处理方法称为表面强化热处理。常用的表面加热方法有以下几种。
电接触加热表面淬火,它是利用触头和工件间的接触电阻使工件表面快速加热,并借其本身未加热的热传导来实现淬火冷却。此法的优点是设备简单,操作方便,工件畸变小,淬火后不需回火。它能显著提高工件的耐磨性和抗擦伤能力,但淬硬层较薄(0.15~0.30mm)。目前多用于机床铸铁导轨的表面淬火。
此外还有火焰加热表面淬火、感应加热表面淬火及激光加热表面淬火等。
(3)化学热处理
化学热处理的方法较多(见表2-3),由于渗入的元素不同,会使工件表面具有不同性能。例如渗碳、碳氮共渗可提高钢的硬度、耐磨性及疲劳强度;氮化(渗氮)使工件表面特别硬,显著提高耐磨性、疲劳强度和耐蚀性;氮碳共渗(又称软氮化)可提高工件表面的耐磨性、疲劳强度和抗擦伤能力等。可根据工件的工作条件和对性能的要求,选用不同的工艺方法。
表2-3 常用化学热处理的特点及应用比较

(4)时效和冷处理
①去应力时效 是指精密零件在半精机械加工后,加热至500~650℃范围内,保温较长时间(常用4~12h),然后在空气中冷却,以消除内应力的热处理工艺操作。
②低温时效(低温去应力退火处理) 是指精密零件在半精磨机械加工后,在油浴或空气炉中,加热至160~220℃,经6~24h保温后,于空气中冷却。其目的在于消除精机械加工及磨削加工产生的应力。精度要求高的零件还要求进行多次的低温时效处理。
③冷处理 要求高硬度(硬度大于60HRC)的合金工具钢、轴承钢工件,淬火、回火后常含有较多的残余奥氏体,而在使用过程中,残余奥氏体会继续转变,使零件尺寸精度发生变化。因此,对于精度要求较高精密零件,为了消除或减少残余奥氏体,零件在淬火后随即冷至-70~-40℃,保持一段时间后再低温回火,精度高的零件也可反复进行多次冷处理,或在更低温度下进行冷处理。
应当注意:只有经过淬火的工件才进行深冷处理。形状简单的工件淬冷后立即放入深冷装置,形状复杂的工件应在淬火后立即低温回火,然后放入深冷装置,以免冷处理时工件中产生的内应力与淬火残余内应力叠加,使工件变形开裂。
2.1.3 机床零件的热处理工艺性
零件热处理工艺性是指在满足使用性能要求的前提下,采用热处理生产的可行性和经济性。机床零件热处理工艺性既涉及机床零件的材料和结构,又与机床零件生产流程和热处理工艺过程各环节密切相关。所以,在机床零件设计时必须充分重视热处理工艺性,合理地选择材料,正确提出技术要求,同时,在制定生产流程时,应合理安排热处理在整个加工工艺路线中的位置,处理好热处理工艺与前后工序的关系,而正确地制定热处理工艺,确保机床零件和产品质量,提高生产效率,降低生产成本,同样是十分必要的。
机床零件的热处理工艺性主要包括淬透性、淬硬性、回火脆性、过热敏感性、回火稳定性、氧化脱碳倾向等。
(1)淬透性
所谓淬透性,是指钢在淬火时获得淬透层深度的能力。它是钢材本身固有的属性,其大小通常以规定条件(指规定尺寸和形状的钢试样,在规定的淬火冷却条件下淬火)下淬透层的深度来表示。规定条件下淬火后钢的淬透层越深,表明其淬透性越好。对于结构钢,一般规定由钢件表面到半马氏体区(即50%区域M组织)的垂直距离作为淬透层深度。
钢的淬透性直接影响其热处理后的力学性能。此外,淬火组织中马氏体量多少还会影响钢的屈强比(σs/σb)和疲劳强度(σ-1)。马氏体量越多,σs/σb越高。对于不允许出现塑性变形的工件,一般都希望屈强比高些,以尽量提高材料强度的利用率。马氏体量越多,则钢回火后的疲劳强度也越高。
钢的淬透性使钢产生尺寸效应,由于零件截面尺寸大小不同而造成淬硬层深度不同,同时也影响淬火件表面硬度,因此必须充分重视材料的淬透性,合理选材,对于大截面或形状复杂的重要零件,应选用淬透性好的合金钢,添加合金元素Mn、Si、Cr、Ni及微量B等提高淬透性,而V、Ti、Mo、W等则起到细化晶粒的作用,它们可保证沿整个截面都具有高强度、高韧性的良好配合,同时减少热处理变形和开裂。因此,应根据钢的淬透性合理安排加工工艺路线。当零件尺寸较大、又受到淬透性限制时,为保证淬硬层深度,可采用先粗加工后热处理,热处理后再精加工。截面差别较大的零件,如大直径台阶轴,从淬透性考虑,可先粗车成形,然后调质,增加淬硬层深度。
总之,钢的淬透性是制定热处理工艺的重要依据。淬透性好的钢淬火时,可选用较缓和的淬火介质和较慢冷却的淬火工艺,以减少零件的变形和开裂倾向。
(2)淬硬性
钢的淬硬性(可硬性)是指钢在淬火后所能达到的最高硬度,即钢在淬火时的硬化能力,它主要取决于钢(马氏体)的碳含量。钢的碳含量越高,淬火后的硬度也越高,其他合金元素的影响较小。因此,在要求工件表面硬度较高时,应选择中碳或高碳钢;对表面硬度要求不高时,一般选择中碳或低碳钢。应注意的是,钢的淬透性和淬硬性是两个完全不同的概念。
(3)回火脆性
淬火钢在随后的回火过程中,当回火温度升高时,钢的冲击韧度变化规律如图2-1所示。由图可见,在250~350℃和400~550℃两个温度区间冲击韧度显著降低,这种脆化现象称为回火脆性。

图2-1 钢的冲击韧度随回火温度的变化
①低温回火脆性 在250~350℃回火时出现的脆性,为低温回火脆性(第一类回火脆性)。几乎所有工业用钢都有这类脆性。这类脆性的产生与回火后的冷却速度无关,即在产生脆性温度区回火,不论快冷或慢冷都会产生此类脆性。
目前还没有办法完全消除第一类回火脆性,通常都是避开此温度范围回火,或采用等温淬火代替淬、回火,或在钢中加入少量硅等合金元素,使脆化温区提高。
②高温回火脆性 在400~550℃范围回火后缓慢冷却所产生的脆性称为高温回火脆性(第二类回火脆性)。这类回火脆性具有可逆性,即将已产生此类回火脆性的钢,重新加热至650℃以上温度,然后快冷,则脆性消失;若回火保温后缓冷,则脆性再次出现,故又称可逆回火脆性。这类回火脆性主要发生在含Cr、Ni、Si、Mn等合金元素的结构钢中。
关于高温回火脆性产生的原因,一般认为与Sb、Sn、P等杂质元素在原A晶界上偏聚有关。Ni、Cr、Mn等合金元素促进杂质元素的偏聚,这些元素本身也易在晶界上偏聚,所以增强了这类回火脆性的倾向。
防止高温回火脆性的办法是:采用先进的冶炼技术(如电渣重熔钢、真空重熔钢等),提高钢的纯净度,尽量减少钢中杂质元素(如S、P等)的含量;或者加入W(1%)、Mo(0.5%)等能抑制晶界偏聚的合金元素;避免在此温度(450~650℃)之间回火;若在此温度范围回火,则回火保温后应快冷(如水冷或油冷)以抑制杂质元素的析出。
(4)过热敏感性
它包括奥氏体晶粒长大,过热、过烧等。钢件加热超过临界温度时,获得奥氏体组织,随加热温度的提高和保温时间的延长,奥氏体晶粒会逐渐长大,不同的钢种,冶炼方法不同,奥氏体晶粒长大的倾向也不同。当钢中含Mn、C、P等元素会促使奥氏体晶粒长大;W、Mo、Cr等元素以及Al、Ti、V、Zr、Nb等微量元素降低奥氏体晶粒长大倾向。
钢在加热时,由于加热温度过高,保温时间过长,奥氏体晶粒会长大,从而引起性能显著降低的现象称为过热;继而当加热温度接近固相线附近时,奥氏体晶界会被氧化或部分熔化,这就称为过烧。过热的重要特征是晶粒粗大,将使钢的屈服强度、塑性、冲击韧度和疲劳性能降低,同时提高钢的韧脆转折温度TK;过热还会使淬火马氏体粗大,降低其耐磨性能,增加淬火变形和开裂倾向。因此,在工业生产中,总是通过各种途径来细化晶粒,达到提高力学性能之目的。
过热可以返修,返修前需进行一次细化组织的正火或退火,再按正确规范重新加热淬火。过烧组织晶粒极为粗大,晶界有氧化物网络,钢的性能急剧降低。这种缺陷无法挽救,工件只得报废。
(5)回火稳定性
所谓回火稳定性,是指淬火钢在回火过程中抵抗硬度、强度下降的能力。由于合金元素阻碍原子扩散,促使淬火碳钢在回火过程中组织分解和转变速度减慢,使回火转变的四个阶段推向更高的温度,使回火后的硬度降低得比较缓慢,从而提高回火稳定性。因而在淬火回火状态下,与碳钢相比,在回火温度相同条件下,合金钢具有较高的强度和硬度;在保持相同强度硬度条件下,合金钢回火温度较高、回火时间较长,内应力消除彻底,故塑性、韧性较高。在工业生产中,对要求内应力消除较完全、强度与韧性配合好的工件,应选用回火稳定性高的合金钢。对于使用温度较高的工件,要选择回火稳定性高的钢种,一般使用温度最高限度在回火温度以下50℃。
(6)氧化脱碳倾向
钢在加热过程中,由于周围氧化气氛的作用,表面的铁被氧化成氧化铁,使钢表面失去原有的光泽,称为氧化。其主要化学反应式为:
脱碳是指钢表面的碳分被氧化成CO、CH4等气体,使钢表面的含碳量降低。其化学反应式为:
式中 (C)——溶于奥氏体中的碳。
氧化使工件表面失去金属光泽,表面粗糙度值增加,精度下降,影响工件尺寸和降低表面质量;同时还使钢的强度降低,其他力学性能也下降,增加了淬火开裂和淬火软点的可能性。脱碳使工件表面碳贫化,从而导致钢件淬火硬度、疲劳性能和耐磨性明显降低。严重的氧化、脱碳会造成工件报废。在各种钢种中,含Si钢的氧化脱碳倾向较大。
在工业生产中,应尽量避免工件的氧化脱碳,重要零件不允许在最终零件上有氧化脱碳层存在。因此,应在生产过程中通过合理预留加工余量,适当安排好加工流程,在热处理工序中,应积极采用各种少(无)氧化脱碳的热处理工艺,控制氧化脱碳,保证工件热处理质量,获得稳定可靠的使用性能。
2.1.4 机床零件热处理工艺性的合理选择
合理选择机床零件的热处理工艺性,主要应考虑以下几方面的内容。
2.1.4.1 机床零件热处理工艺性的结构设计
在机床零件的设计过程中,必须考虑零件的结构、形状、尺寸等在之后热处理工艺中能顺利实施,而不致产生大量废品或次品。
在实际生产中,设计人员往往仅片面、孤立地使零件结构形状适合部件机构的需要,忽略了零件在加工或热处理过程中,因结构形状不合理而导致热处理淬火变形、开裂,而使零件报废。为此,在设计淬火零件结构形状时,应掌握以下原则。
①避免尖角和棱角 零件的尖角、棱角处是淬火应力最为集中的地方,往往导致淬火裂纹。因此,在设计带有尖角、棱角的零件时,应尽量加工成圆角、倒角以避免开裂。一般原则如图2-2所示。

图2-2 避免尖角设计实例
②避免截面突变(断面薄厚相悬殊) 厚薄悬殊的零件,在淬火冷却时,由于冷却不均匀而造成的变形、开裂倾向较大。可采用开工艺孔、加厚零件太薄部分、合理安排孔洞位置或变不通孔为通孔等方法加以解决,如图2-3所示。

图2-3 避免截面突变,防止工件淬火变形开裂实例
③采用封闭、对称结构 开口或不对称结构的零件在淬火时应力分布亦不均匀,易引起变形,应改为封闭或对称结构。图2-4(a)为生产上经常碰到的弹簧卡头,其头部都采用封闭结构;也可在加工成形后,采用铜焊使形成封闭结构再淬火,在淬回火后再切开槽口。而图2-4(b)所示为一镗杆截面,要求氮化时变形极小。原结构设计是在镗杆的一侧开槽,结果变形较大;后修改设计,在另一侧也开槽,使零件形状呈对称结构,结果减少了镗杆在热处理时的变形。

图2-4 采用封闭、对称结构实例
④采用组合结构 某些有淬裂倾向而各部分工作条件要求不同的零件或形状复杂的零件,在可能条件下可采用组合结构或镶拼结构。图2-5所示为一磨床顶尖,该顶尖要求有高的热硬性。原设计方案采用高速钢W18Cr4V整体制造,在整体淬火后,顶尖出现了裂纹。后修改设计采用组合结构,顶尖部分仍采用W18Cr4V制造,但尾部换用45钢,分别经热处理后,采用热套方式配合,既解决了顶尖淬火开裂,又节约了高速钢钢材,效果较好。

图2-5 采用组合结构实例(磨床顶尖)
⑤细长零件,其长径比不宜太大 如机床丝杆、细长轴等,为避免或减少变形,在热处理时应在井式炉内吊挂加热,因此其形状应便于吊具装夹。
⑥零件应具有足够刚度 其目的是保证零件在加工特别是热处理过程中,不会发生畸变,必要时可附加加强筋。
⑦热处理零件最终热处理时表面应清洁,并具有较低粗糙度 一般淬火零件粗糙度Ra≤3.2μm;渗碳零件Ra≤6.3μm;渗氮零件Ra≤0.80~0.10μm。
⑧拼焊零件焊缝处,不得要求淬火 因拼焊零件淬火时,焊缝处易开裂。
另外,零件结构形状和热处理工艺方法及所选用的设备有一定关系。例如,细长零件应采用井式炉吊挂加热。热处理工艺参数不仅应根据选择的材料来确定,而且还应按零件形状尺寸因素来调整。淬火冷却时,细长和圆筒形零件应按长度方向淬入介质;圆盘状零件应径向淬入并横向左右移动;薄片形长刀片应使刃口同时入淬火液;带各种孔眼、凹槽的零件应选择使淬火液易于流动的方向淬火。如图2-6所示。总之,零件结构与所需进行的热处理工艺应相互配合适应。

图2-6 工件投入淬火介质的方式
2.1.4.2 机床零件热处理工艺的选择
若材料和热处理工艺选择不当,往往造成使机床精度保持性降低、零件寿命短、工艺复杂、成本提高。材料及热处理工艺与产品结构、制造工艺、使用寿命和成本有密切的关系,要做到合理选择,必须对机床的结构性能、零件的服役条件、冷热加工工艺要求等进行全面了解,然后再根据不同材料及热处理工艺的特点,通过综合分析对比确定下来。
机床零件所选用的材料,必须保证其有足够的刚性和强度,同时应有较好的切削加工性能。其热处理方案选择的一般原则如下。
①强度要求不高的工件,多采用碳素结构钢制造,一般都应该进行正火处理(包括碳素铸钢件)。
②为了获得较好的切削加工性和低的表面粗糙度,工具钢(碳素和合金)应进行球化退火,低合金结构钢应进行正火处理。淬硬性好的钢材,正火后还应进行高温回火。
③对于强度要求较高及综合力学性能较好的钢件,应采用调质处理。
④为减少变形,对于淬火及表面淬火的钢件,可采用调质处理作为预先热处理;感应淬火的齿轮也可在粗机械加工后采用感应正火。
⑤对于整体要求高强度、又要求较高耐磨性的零件,可整体加热淬火,并回火至适宜的硬度。如轴承钢及合金工具钢制零件,可整体淬硬至59HRC以上。
⑥对于弹簧钢制零件(冷拔弹簧钢丝件除外),均应进行整体淬火回火至42~48HRC。
⑦不适合局部淬硬的小零件如短轴、销子、螺母及长度小于100mm的螺钉等,需整体淬硬。
⑧对于诸如内外表面要求淬硬的套、蜗杆、齿轮、结合子等零件,由于要求采用表面淬火淬硬的表面较多,应改为整体淬硬。
⑨对于多孔、薄壁、形状复杂的零件,采用表面淬火加热不易均匀、质量难以保证,应采用整体淬火、回火。如锥度大的伞齿轮可采用淬火压床淬火。
⑩对于诸如内六方、内四方螺钉头部、各种扳手头部、锻锤楔铁等靠近端部有强度、硬度要求的工件,或如上所述不宜采用表面淬火时,可采用盐浴加热局部淬火回火。
对于仅表层要求较高的耐磨性和强度,形状不复杂的零件,如轴、套的外圆表面、机床导轨及滑枕表面、直径大于50mm的内孔表面等,应采用表面淬火。大模数齿轮齿面也采用单齿表面淬火。
对于局部要求较高耐磨性和强度、形状不复杂、心部强度要求不高的零件,如轴及螺钉的六方、四方头部,联轴器齿部,锁紧螺母的扳手孔及槽、蜗杆齿部等,可采用表面局部淬火回火。上述零件基本上为深层加热,淬硬层较深。
高精度、高耐磨性及疲劳强度要求高的零件,如中等以上载荷的齿轮、蜗杆、主轴、套等精密零件及耐磨性要求高的零件,可采用渗碳或碳氮共渗+淬火+低温回火。
高精度、高耐磨性、高疲劳强度而载荷轻的齿轮、蜗杆、丝杆、主轴、套等精密零件,可采用渗氮或氮碳共渗。对于精度高、载荷轻、形状复杂、淬火易变形开裂的零件,如花键套、多孔分度盘等,也可采用渗氮处理。
对于精密细长零件,粗机械加工后应进行去应力退火;硬度大于60HRC的轴承钢、合金工具钢制造的主轴、丝杠和镶钢导轨等精密零件,整体淬火后应进行冷处理。所有精密零件在精磨以后应进行一次或多次低温时效处理。
影响机床精度的铸铁件,在粗机械加工后应进行时效处理;有精度要求的焊接件,焊接后应进行高温回火处理。
2.1.4.3 机床零件热处理技术要求的确定
热处理技术要求,是零件设计者在材料确定后提出的,并应在图样上标注出来。机床零件热处理技术要求,一般是热处理质量的检验指标,主要包括硬度和其他力学性能指标,淬硬层深度,显微组织的控制标准,热处理允许的变形量等。
2.1.4.4 热处理工序的安排与热处理工艺性
一个机床零件的产生是由各种加工工艺配合的结果。在正确设计和合理选材的基础上,只有合理安排各加工工艺流程,才能生产出符合技术要求、成本低的零件。各加工工序之间有着密切的联系和影响,特别是热处理工序,其他加工工序对热处理工艺性和热处理质量都有重要的影响。
(1)热加工与热处理工艺性
正确的热加工(如轧制、锻造等),可显著改善金属材料的性能,消除或减轻原材料中存在的各种缺陷,如气孔的焊合、粗大树枝晶和柱状晶的破碎、非金属夹杂物形态和大小及分布的改变等。
①铸造工艺与热处理工艺性的合理配合 铸造工艺与热处理工艺性之间的关系十分密切,其合理配合可有效消除铸造应力,均匀与改善组织,提高力学性能,从而满足使用要求。
普通灰铸铁是工业上应用最为广泛的铸铁,为消除铸件冷却过程中产生的内应力,防止铸件在后续加工工序中产生变形与裂纹,常需进行低温退火(即时效处理)。特别是形状复杂的高精度机床的重要铸件(如机床导轨等),在机械半精加工后,还应进行第二次时效处理。机床导轨一般采用高强度灰铸铁制造,为提高导轨的耐磨性和机床精度的保持性,延长使用寿命,常需进行表面淬火(感应加热、火焰加热表面淬火等),以获得一定深度的硬化层。
球墨铸铁生产中常用的热处理方法有退火、正火、淬火、回火及等温淬火等,由于其石墨为球状,对基体的破坏作用可降至最低程度,以致基体的作用可得到较充分发挥,因而几乎所能采用的热处理方法都可用于球墨铸铁,使其力学性能得到充分的改善。
碳素钢及低合金铸件常采用退火、正火、高温回火等工艺,以消除应力、均匀及改善组织。对于高合金钢铸件,为消除枝晶偏析及驱逐因固溶于钢中的有害气体氢,常采用高温长时间的扩散退火等。
②热变形加工与热处理的合理配合 热变形加工的加热温度、加热速度、终锻(轧)温度、冷却方式等都会影响金属材料的组织和性能以及残余应力的分布。锻轧温度过高,或在临界变形度范围内形变,就会导致形成粗大晶粒,并增加淬火后变形开裂倾向;终锻(轧)温度过低,也会增加残余内应力,进而使材料内部出现微裂纹,最终在淬火时会开裂。若在热加工时未能把碳化物不均匀性和方向性基本消除,就会使钢的热处理工艺性恶化,如过热敏感性增加、淬硬性降低、变形增大等;若精锻后零件表面上出现脱碳层,在后续热处理过程中易在零件表面形成高残余拉应力,甚至造成开裂。总之,不正确的热变形加工,都会使工件的热处理质量变差,如组织不均匀,硬度不均匀,力学性能下降。冷却方式也是造成零件开裂的原因之一。
③焊接与热处理的合理配合 焊接后的工件在焊缝处为铸态组织,在热影响区则可能存在过热组织,焊缝中还有可能有夹杂、微气孔等缺陷,并在构件中还存在较高焊接应力。所以焊接件应进行退火或正火来消除内应力及改善组织。复杂的焊接件,在焊接过程中还需进行中间退火或正火。
(2)冷加工与热处理工艺性
①冷变形加工与热处理的合理配合 冷挤压、冷冲压、冷拉、冷镦等冷变形压力加工前,必须经过良好的预先热处理,以获得均匀且具有良好塑性的组织(细晶粒及粒状渗碳体),同时在加工成形过程中或最后还需进行消除加工硬化或残余内应力的正火或退火处理。对于形状复杂的精冲压零件,只有球化退火组织才能获得高的精度和表面粗糙度。但球化组织的抗拉强度较低,当强度达不到设计要求时,还需用热处理方法来提高。
②切削加工性与热处理的合理配合 切削加工性的改善与热处理工艺性的关系更是密不可分。切削加工性体现在被加工零件的表面粗糙度、切削力的大小以及切削刀具的使用寿命等方面。金属材料的组织和性能对切削加工性有着重大的影响。不同材料在不同切削加工方式下表现出来的切削加工质量是不一样的,如表2-4所示。
表2-4 几种常用结构钢热处理后组织、硬度和表面切削加工质量的关系

为改善切削加工性,过共析钢及共析钢应采用球化退火,中碳钢可根据不同要求采用正火、调质或等温处理。经正火处理的低碳钢由于硬度达不到良好切削加工表面粗糙度时,可采用喷雾冷却、不完全淬火等方式来进一步提高硬度,改善切削加工性。对于难切削加工的奥氏体不锈钢、奥氏体耐热钢、耐磨钢等,仅改变组织很难改善可加工性,则应从切削加工工艺本身的革新来解决,如采用电解液加工、电火花加工、等离子切削等方法。
钢的组织对磨削过程也有影响。表面存在粗大的网状碳化物,过量残余奥氏体,表面脱碳层等均易导致磨削裂纹的产生。另外,磨削裂纹的产生还往往与磨削工艺规范直接相关。所以,解决磨削裂纹,既要求工件有良好的组织,又需根据不同情况制定适宜的磨削工艺。
在大批量生产中,若热处理生产条件稳定,质量控制及检测技术较好,可总结出零件在热处理过程中尺寸及形状变化规律,从而可修改或制定适当的工艺公差。利用工艺公差来事先补偿热处理工艺的尺寸及形状变化,保证零件质量。
还需强调的是,零件的切削加工质量对热处理工艺性也有很大的影响。如零件的车削加工表面太粗糙、刀痕过深,将会引起缺口效应,在淬火冷却时就会因缺口处局部应力过大而产生淬火裂纹。
(3)热处理工序的合理安排
一个零件从原材料或毛坯到零件完成和装配要通过许多道次的冷、热变形加工工序,热处理工艺在整个工艺过程中如何安排,对零件的工艺性有很大影响,不同零件在工艺过程中热处理工序安排是不同的。
①预先热处理工序位置的安排 它主要指退火、正火、调质等工序。这些工序主要安排在毛坯生产(指铸、锻)之后,切削加工之前,有时也安排在粗机械加工之后,精机械加工之前。
a.退火、正火工序。一般安排在毛坯生产之后,切削加工之前。其加工工艺流程为:毛坯(铸或锻坯)→退火或正火→切削加工→最终热处理等工序。
对于精密零件,为消除切削加工造成的附加内应力,在切削加工工序之间往往还安排一次去应力退火。去加工工艺流程为:毛坯(铸或锻坯)→退火或正火→粗机械加工→去应力退火→半精机械加工→后续其他工序。
b.调质工序。一般安排在粗机械加工之后,精或半精机械加工之前。一般不安排在粗机械加工之前进行调质,以免坯料粗糙表面的氧化、脱碳层影响调质质量。
调质件的加工工艺流程为:下料→锻造→退火或正火→粗机械加工→调质处理→半精机械加工或精机械加工→成品或继续后续工序。
坯料在调质处理时,会产生较大的氧化、脱碳及变形,因此调质处理前的粗机械加工必须留有足够的加工余量(一般视材质零件直径不同单边留有2~4mm的加工余量)。例如38CrMoAlA钢加热时脱碳倾向大,为此其加工余量应在正常范围基础上还应再增加50%以上。此外,为控制调质件的变形量,在工艺上应规定允许的变形量,若超过就应增加校直工序。调质处理前的加工余量如表2-5所示。
表2-5 调质件的加工余量(直径)

对于灰铸铁件、铸钢件、某些钢轧制件及锻钢件,经退火、正火或调质处理后,往往不再进行最终热处理,这些工序也就成为事实上的最终热处理工序。
②最终热处理工序位置的安排 零件经最终热处理后,由于硬度高,只能进行磨削加工,故工序位置应尽量靠后,一般均安排在半精机械加工之后,磨削工序之前进行。
a.淬火工序。
•整体淬火件的加工工艺流程一般为:下料→锻造→退火(或正火)→粗机械加工→半精机械加工→淬火、低温或中温回火→磨削加工→成品。
•感应淬火件的加工工艺流程一般为:下料→锻造→退火(或正火)→粗机械加工→调质处理→半精机械加工→感应淬火、低温回火→磨削→成品。
由于零件淬火后往往会产生较大的变形,若零件淬火加热保护条件不好,还会出现氧化、脱碳现象。因此,需根据具体热处理条件预留一定加工余量,以备最终热处理后再经磨削加工去除。淬火件预留磨量如表2-6~表2-10所示。
表2-6 平板类零件预留余量和淬火变形允差

表2-7 轴、杆类零件预留余量和淬火变形允差

注:1.粗磨后需人工时效的零件应较上表增加50%。
2.此表适用于断面均匀的全部淬火件,特殊零件应另行协商。
3.淬火长度短于全长1/3以下时取下限;大于1/3以上时按全长处理。
4.ф80mm以上短实心轴可取下限。
5.表面淬火件可取下限。
表2-8 套类零件预留余量和淬火变形允差


注:1.畸变量是指淬火后的最大尺寸与名义尺寸之差。
2.套的截面变化很大时,应按表中规定适当增加20%~30%。
3.碳素钢的加留量应取上限,其畸变量也允许随之增大。
4.套的内孔大于80mm的薄壁零件,粗加工后应经正火处理,以消除应力和减小畸变。
表2-9 花键轴淬火(包括渗碳淬火)变形允差

注:振摆仅指花键部分,其余部分仍按一般轴类件考虑。
表2-10 蜗杆轴淬火(包括渗碳淬火)变形允差

表面淬火件由于仅表面硬化,故其变形较整体淬火件要小。此外,表面淬火件为提高其心部力学性能及获得细小的马氏体表层淬火组织,常需先进行正火或调质处理。由于调质处理后的组织,其比体积比正火后的更接近淬火组织,因而预先热处理采用调质处理更有利于减少表面淬火后零件的变形。若感应加热表面淬火之前不加调质处理工序,锻造后的预先热处理就必须采用正火处理。若正火后硬度偏高,切削加工性不佳时,可在正火后再进行高温回火。
b.渗碳淬火工序。渗碳分为整体渗碳和局部渗碳两种。当渗碳淬火件局部不允许有硬度时,应在设计图样上注明。防渗部位可镀铜或采用多留加工余量的方法,待零件渗碳后,淬火前再去除该部位的渗碳层。局部不渗碳处的加工余量应根据零件设计所要求的渗碳层深度来确定。渗碳淬火件的加工余量如表2-11所示。
表2-11 切去渗碳层的加工余量

注:合金渗碳钢切除渗碳层的加工余量应增加0.5~1.0倍。
渗碳淬火件的一般加工工艺流程为:下料→锻造→正火→粗机械加工→半精机械加工→局部渗碳时,对于不需渗碳部位,采取镀铜保护(或预留去除渗碳层余量方法)→渗碳→(对于预留去除渗碳层余量者,再经切削加工去除不需渗碳部位的渗碳层)→淬火+低温回火→磨削→成品。
c.渗氮工序。由于渗氮温度低,且渗氮后不需淬火,故零件变形小,渗氮层硬而薄(渗层一般小于0.6mm),故其工序位置应尽量靠后,一般渗氮后只需精磨或研磨,为防止因切削加工产生的残余应力引起渗氮件变形,在渗氮前常需进行去应力退火。又因渗氮层薄而脆,工件心部必须有较高的强度才能承受载荷,故一般应先进行调质处理。调质后形成的细密均匀的回火索氏体组织,可提高工件心部的强度和韧性,防止出现异常的渗氮层组织及脆性,从而可获得良好的渗氮层。
渗氮件的加工工艺流程一般为(以38CrMoAlA钢为例):下料→锻造→退火→粗机械加工→调质处理(注意:其后需切试片进行金相组织检验,表面铁素体量应小于5%)→半精机械加工→去应力退火(注意:其加热温度应小于调质处理的高温回火温度)→粗磨→渗氮(注意:带试片,以利于渗氮后金相组织及渗层深度检验)→精磨或研磨(注意:对高精度零件,为避免研磨过程产生的附加应力造成工件变形或开裂,应在两次精磨或研磨之间增加一次低温稳定化处理工序)→成品。
对需精磨的渗氮件,粗磨时直径应留0.10~0.15mm的加工余量;对需研磨的渗氮件,则只需留0.05mm的加工余量。
零件不需渗氮部位可镀锡(或镀镍)保护,也可留1mm防渗加工余量,渗氮后再磨去。
d.其他情况时的加工工艺流程的合理安排。在实际生产条件下,常因某些特殊需要,如零件毛坯尺寸的改变或者为了防止工件的淬火变形或开裂等,在制定具体加工工艺流程时,热处理工序还会有所变动,为此还应根据具体情况进行调整。
•如采用型材毛坯,则锻造及其后的退火或正火等工序便可省去。
•对于细长轴类和形状复杂的零件,在粗机械加工成形后,安排一道去应力退火工序,以消除切削加工引起的应力,对减小淬火变形十分有利。
•对于一些精密零件,为消除切削加工造成的残余应力,应同渗氮件一样,在粗机械加工后可穿插去应力退火或时效(或称稳定化)处理以减少变形。而对于诸如精密机床主轴、丝杠等需要精磨的精密零件,在最终热处理及粗磨后,一般安排1~2次时效处理(注意:处理温度应低于回火温度,时间应在10h以上,一般放在油浴炉内进行,习惯又称油煮定性),以消除磨削应力,稳定工件尺寸,防止随后发生变形。对于精密丝杆,有时还采用先整体淬火、回火,再将螺纹磨削成形,以保证精度,防止开裂。
•适当调整加工工艺流程的顺序,以利于减少工件变形。
一45钢制锁紧螺母(见图2-7),要求四个槽口部分的硬度在35~40HRC。当槽口、内螺纹等全部加工后,再整体淬火、回火,槽口硬度虽可达到要求,但内螺纹变形较大(涨大),不能保证精度;若先热处理后再切削加工,则又嫌硬度较高,切削加工困难。因此,通过将热处理方法及工序位置调整来解决这些矛盾。其加工工艺流程如下:下料→调质处理(硬度25~30HRC)→加工槽口→槽口高频感应淬火(硬度达35~40HRC)→加工内螺纹。

图2-7 锁紧螺母
这样,既满足了槽口的硬度要求,又保证了螺纹的精度。
又如,图2-8所示是45钢制齿轮,它有6个ф35mm孔靠近齿根。若先加工出这些孔再进行高频淬火,则齿部靠近ф35mm孔处的节圆直径将会变小,因此只能在高频淬火后再钻这6个孔。

图2-8 45钢齿轮
再如图2-9所示的镶条,选用20Cr钢,渗碳层深度为1.3~1.7mm,淬火、回火后硬度为56~62HRC。由于一面有配作孔,镶条在渗碳后必须将配作面的渗碳层加工掉,结果镶条两面的碳含量不同,淬火时体积变化不同。渗碳面碳含量高,淬火后表面残余压应力较大,配作面去碳后碳含量低,残余压应力较小,结果造成很大变形。由于校直困难,影响磨削加工。如改成按下述加工工艺流程加工,可减少变形:下料(两件)→粗机械加工→渗碳→开切口→淬火、回火→切开(分成两件)→磨削,配作。

图2-9 镶条
总之,合理的热处理工序安排,既可达到技术要求,又可减少零件的变形。
以下就金属切削机床典型零件的热处理特点作一分析说明。